- Liz Taylor
- Feb 21, 2023
- 5 min read
Updated: Apr 5, 2023
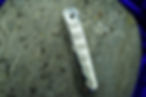
So what is a hallmark?
Hallmarking is a process whereby precious metals are tested for their purity and stamped with an official mark of authenticity to indicate their quality. The hallmarking system was introduced in the 13th century by Edward I, who believed that it was important to guarantee th
e quality of jewellery being made and sold in the kingdom. It is a legal requirement in the UK that any item of jewellery containing of a particular weight of gold, silver or platinum must be hallmarked. Although it is a system that has been around for centuries, the British jewellery industry is now facing a unique challenge in a time of high precious metal costs - the ‘hallmarking tax’. While there is general consensus that hallmarking is a necessary safeguard for consumers, there are also various cons of these regulations. This article puts forward the arguments from the perspective of the government, consumer and jeweller.
Hallmarking is a part of the legal framework governing the jewellery industry in the UK. It is a process that has been used for centuries to ensure that precious metal jewellery meets the standards set by a governing body. It is a highly regulated process. In order to obtain a hallmark, the metal must first be sent away to a laboratory where it is tested and assayed by experts. This process involves a number of steps, including weighing, measuring, and X-ray imaging, in order to determine the purity of the metal. The metal is then given a stamp or laser mark of approval that indicates whether it meets the required standard.
Hallmarking is a legal requirement in some, but not all countries. From the perspective of the governments in which hallmarking is required, regulations provide an essential layer of consumer protection and ensure that consumers are getting the quality of product they expect. The regulations also provide a level playing field for jewellers, ensuring that all jewellery is subject to the same standards, regardless of the size or reputation of the business.
The Consumer
Hallmarking acts as a form of protection against fraud. Because the item has been tested and confirmed to be of the stated metal content this protects the consumer against any false claims made by the seller. It allows the consumer to ensure that it has been accurately priced. Furthermore, the hallmarking process can help detect any irregularities or falsification of materials, and helps to ensure that the item will not deteriorate over time. It provides a record of ownership should the item ever be lost or stolen, allowing the consumer to prove that the item was theirs, should the need arise.
By providing consumers with a guarantee of quality, it offers them peace of mind when making a purchase.
The Jeweller
From the perspective of jewellers, hallmarking regulations can provide a sense of trust and credibility to their business. The mark of authenticity provides customers with tangible proof of quality, making them more likely to trust the jeweller and make a purchase. Additionally, hallmarking regulations provide a sense of assurance to jewellers, as they know that their products are being tested for purity and safety. It helps to protect the reputation of the British jeweller and the craftsmanship of their products.
That said, some see hallmarking as a tax on the British jeweller because it adds an additional cost to their products. They must pay a significant fee to the Assay Office, which is the government body that regulates hallmarking in the UK. The hallmarking process is labor intensive and requires a trained professional to assess the quality of the metal and then stamp it with a mark of authenticity. This cost is then passed on to the consumer. A fee is also charged to cover the costs associated with the administration of the system. This fee is not charged in other countries, meaning that British jewellers have to pay and charge more for their supplies than their international counterparts. This additional cost that puts them at a disadvantage and makes it harder for them to compete in the global market. It is also a barrier to entry for new businesses looking to break into the jewellery industry. The cost of the tax puts off many potential entrepreneurs, even though they may be skilled in producing jewellery. This can make it difficult for the industry to grow and develop.
The Jewellery Industry
This tax is also a burden on the British jewellery industry, which is already struggling with the high cost of precious metals. It adds an extra layer of expense to jewellery production, making it even harder for businesses to make a profit. This is why many British jewellers are turning to alternative metals, such as stainless steel and copper, as a way to reduce costs and increase their margins. It puts British jewellers at a disadvantage in the global market and is a tax that may need to be reconsidered in order to ensure the long-term sustainability of the British jewellery industry.
Summary
In summary, hallmarking regulations provide an important layer of protection for consumers, whilst also ensuring that jewellers are able to operate in an environment of trust and credibility. Although there is a cost associated with hallmarking, many consumers might believe it is worth it for the reassurance it offers. They are able to invest in jewellery with confidence, knowing that their purchase is of the highest quality. Hallmarking helps to protect the industry as a whole by ensuring that all jewellery is of an acceptable standard.
However the burden for smaller businesses may prevent them from producing innovative designs in precious metals, and can potentially put them out of business.
How can independent jewellers limit the financial burden of hallmarking?
1. Considering using an online hallmarking service. This will usually be cheaper than the traditional route of sending pieces to the Assay Office.
2. Make use of bulk hallmarking services. Many Assay Offices offer discounts for bulk hallmarking and some jewellers have even formed hallmarking groups to receive further discounts.
3. Look into hallmarking schemes that provide lower fees. These may be available in certain regions or for certain types of jewellery.
4. Try to source your metals from suppliers who can provide pre-hallmarked metals. This will save you the cost of hallmarking the metal yourself.
5. Never send a single item for hallmarking. Using a 'batch' hallmarking process. This means that all of the items in a batch will be hallmarked in one go, meaning you will only have to pay for one set of assay fees. Keep a stock of ‘blanks’ for rings or bangles which can go in the packet even if you don’t need it at the time. You can then fabricate into finished items when you need.
Ultimately, it is up to the government to decide whether the benefits of hallmarking outweigh the potential drawbacks. It does add extra cost for the UK jewellers, but it is a process that consumers value, and the regulations will not change for the foreseeable future. My opinion is that it is better to embrace the positives and find ways to keep the process affordable. Afterall, there is nothing more satisfying than seeing your own personal makers mark on a verified quality piece of jewellery, which will be a loved item and heirloom for many years to come. Get a sample of gold or silver assayed with a beautiful, legible ‘display mark’, and keep it in your studio to show customers. Have a copy of the legal notice explaining hallmarking to give to customers when receiving their items. It breaks down the meaning of each component of the mark and will certainly be of interest to them, supporting the credibility of your work and the process, ultimately adding value to the piece that you have created for them.